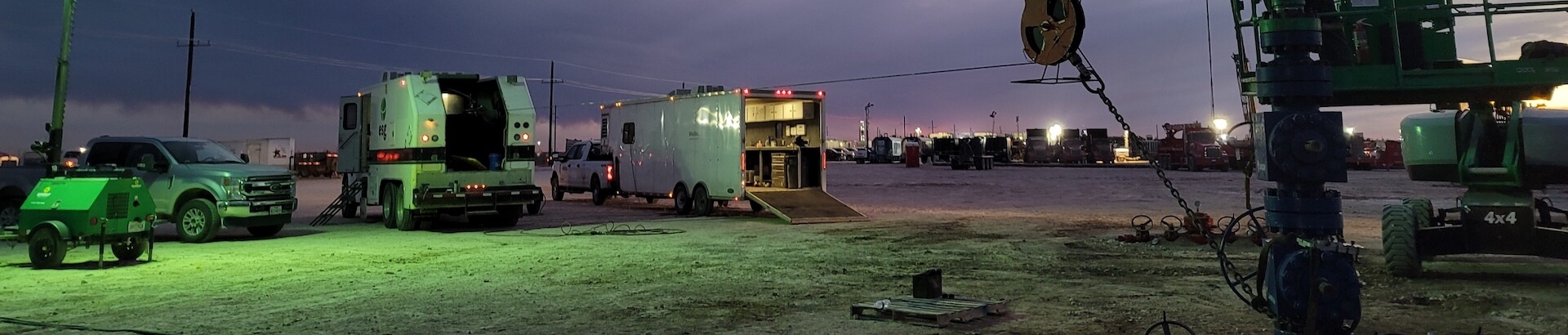
Use of a variable velocity model improves accuracy of microseismic analysis for caving applications
An advanced 3-D raytracing velocity model was developed to account for complex geology and progression of the void during caving operations at a block cave mine in British Columbia. Implementation of the improved velocity model resulted in an approximately 50% reduction in microseismic event location error, enabling mine operators to more reliably track the caving front as it progressed.
As the economics of bulk mining methods such as caving become much more attractive, such operations also introduce new challenges for mining engineers. Paramount to these challenges is the lack of access to the caving front.
Microseismic monitoring provides indirect visualization of the cave front where no visual inspection would normally be possible, improving cave assessment and management. High resolution microseismic monitoring has proven to be one of the most effective ways to understand cave growth and track the progression of the cave front over time.
Background
To assess the progress of a cave, it is critical that microseismic event location and interpretation be as accurate as possible. Inaccuracy in event location can often be traced to the use of an inadequate velocity model. A single velocity model can be used to represent a homogeneous isotropic material, in which all seismic energy would propagate outwards from the source with a 3D spherical wave front. Such a model has been shown to work well in many hard and soft rock mines, however in many cases, a layered velocity model is used to account for the different geological layers within a rockmass. Further complicating velocity modeling in caving operations is the existence and growth of a massive void (cave) in the centre of the sensor array. The void results in signal attenuation and longer travel paths from seismic sources to the surrounding sensors, further rendering a simple velocity model less effective.
ESG Solution
ESG developed a 3D ray-tracing algorithm to account for voids created during caving operations. This 3D algorithm can account for the changing volume of the void over time, as well as any significant heterogeneous geology with different properties and wave velocities in and around the mining zone. The 3D ray-tracing model was applied to microseismic data collected using a 57-channel ESG monitoring system installed at the New Gold New Afton block caving operation located 8km west of Kamloops, BC (Figure 2).
An example of the seismic wave front propagation through a heterogeneous rock mass with a cave zone is shown in Figure 3. In this case, the model has been adapted to account for the effect of the cave zone as well as differences in geological units throughout the mine. These geological units exhibited elastic properties that varied by up to 10% from each other. As shown in Figure 3, the isolines are observed to be significantly affected by the cave zone (grey circle) as well as the different geological domains with irregular boundaries. Applying this algorithm and modifying the cave geometry in the velocity model as it progresses significantly improves the location accuracy of seismic events. For this calibration blast example, the algorithm was found to reduce the location error by approximately 50%.